Plywood is inexpensive, simple to apply, and looks fantastic when done right. One of the most common problems associated with plywood is the rough, jagged edges and tear-outs that emerge from cutting through the thin veneers. Nothing is more annoying than working on a clean job, only to have your lines frayed and damaged. So how do you prevent plywood from tearing out with a CNC router?
Here are 6 top ways to prevent plywood tear-out:
- Invest in quality plywood
- Choose the right blade and face
- Use a zero-clearance insert at all times
- Scoring the woodcut line
- Tape the wood fibers around the cut to keep them in place
- Begin by cutting from the end
Plywood tear-out can be prevented if you employ the right equipment and procedures and devote the right amount of time. Hang around if you’re tired of putting all your efforts into a project, only to have it damaged by plywood tear-out. This article presents some proven ways you can fix and prevent plywood tear-out.
What Causes Plywood Tear-Out?
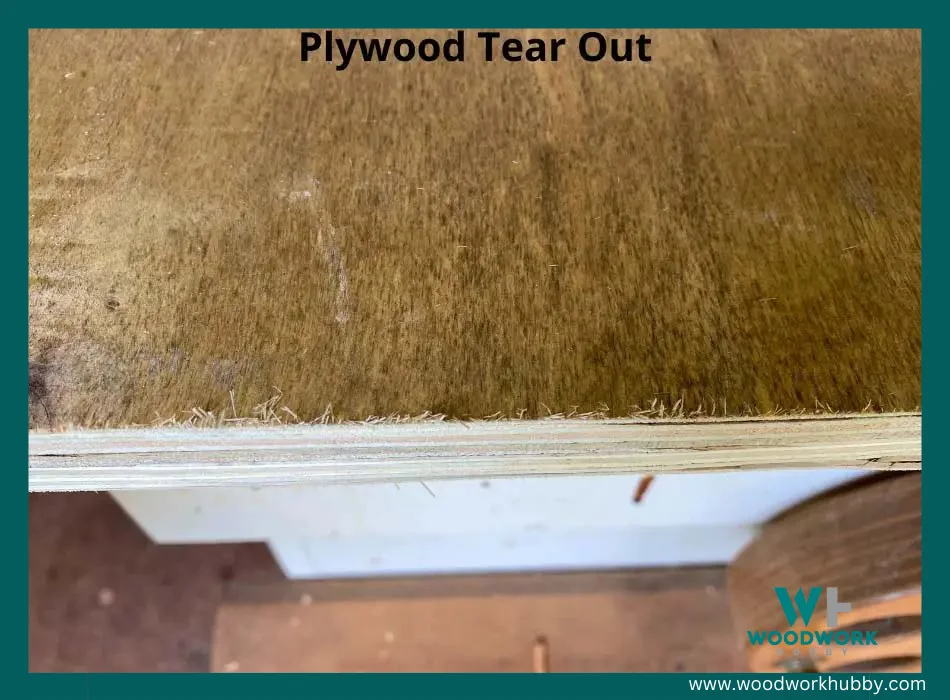
When you trim across the grain, you get a plywood tear-out. Since the fibers don’t get anchored by those around them when they receive a hit, they naturally protrude themselves. It drives them out of the path and takes your nice clean edge with them.
When cutting plywood, three primary factors contribute to tear-out. They are as follows:
- Face Veneer- The low structural strength of the plywood causes the thin face veneer to tear readily. Plywood with a thicker face veneer tears out less because the wood fibers can support one other, although this does not prevent the risk fully.
- Friction- It is the most prevalent catalyst of slivers breaking off, with the blade edges grinding against the end grain at the cut’s edge. Even though most blades have offset teeth to reduce friction, the edge of the toothbrushes is against the end grain. It’s particularly the case with lower-quality blades with less carefully honed teeth.
- Dull Blades- Blades start to deteriorate as soon as we use them and continue to degrade until they are changed. The blade loses its capacity to sever wood fibers as it becomes blander, requiring it to apply more pressure on the fibers before they get severed. Tear-out occurs if the tension holding the fibers together is less than the pressure exerted by the blade’s teeth across the strands.
Something that works in tandem with all three of them is the lack of support the face veneer’s wood grain provides in keeping it from moving (tearing out) rather than cutting. To eliminate tear-out, you must emphasize two factors: how well the fibers are supported and how strenuous the impact on the fibers is.
Top Six Tips to Prevent Tear-Out When Cutting Plywood
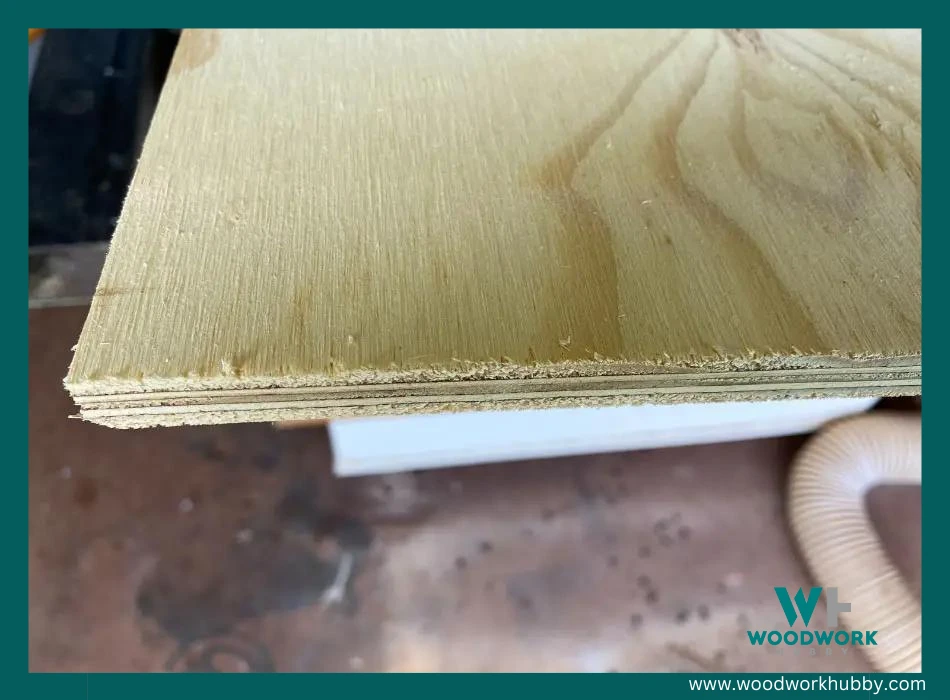
1. Invest in quality plywood
Not every plywood is made to the same parameters. Make sure you inspect your sheet of plywood before purchasing it. Look to see whether the board is twisted or if there is any evidence of water damage. You’ll have to look closely because this won’t be obvious at your local lumberyard.
Quality plywood is heavier. Be sure to read my article on how much plywood weighs.
Also, be cautious when using a sheet of plywood that has been lying in your garage or cellar for a long time. If there’s a chance that water, or even moist air, has come into touch with the plywood, the layers are far more likely to rupture. When cutting, it’s more prone to tear out.
If you’re working on a project that demands a high-quality finish, try purchasing brand-new plywood with tight sealing. However, even fresh plywood will tear to a certain extent.
2. Choose the right blade and face
Innately, you would prefer to use a fine-tooth blade that can cut plywood effectively. These feature more teeth per inch and a higher bevel angle, allowing them to slash through the plywood. You may not need a pricey specialty blade on the table saw, though they can be handy. Simply ensure you’re using a high-quality combination blade with a minimum of 40 tooth blades.
Finally, slice the plywood in such a way that the blade penetrates the wood on the show face. It requires placing the wood on a circular saw with the good side facing upwards on a table saw.
3. Use a zero-clearance insert at all times
The best technique to minimize tear-out, regardless of the tool you utilize, is to envelop the blade or the bit with a zero-clearance surface. It will work whether you’re using a bandsaw, drill press, miter saw, or table saw. A zero-clearance insert leaves the minimum amount of open space around the blade, allowing the wood fibers bordering the cut to be supported optimally.
4. Scoring the woodcut line
When an impact occurs, the top and bottom veneers shatter off in an unanticipated manner, giving tear-out its rugged appearance. So, one approach to avoid the rough edges is to cut the fibers where they can be controlled. They’re going to snap someplace, so you might as well point them in the right direction.
A straight edge and sharp blade could be used to cut across the grain, or if you are cutting close enough to an edge, a marking gauge will do the job quickly. You can even cut your sections oversized, score them, and then trim them to size. Because you can only score one side of the workpiece, ensure your cut gets well positioned so that the good side of the blade is on the intended side.
5. Tape the wood fibers around the cut to keep them in place
Since tear-out happens when fibers get stretched in all dimensions, you can keep them in place by applying painter’s tape across the cut line.
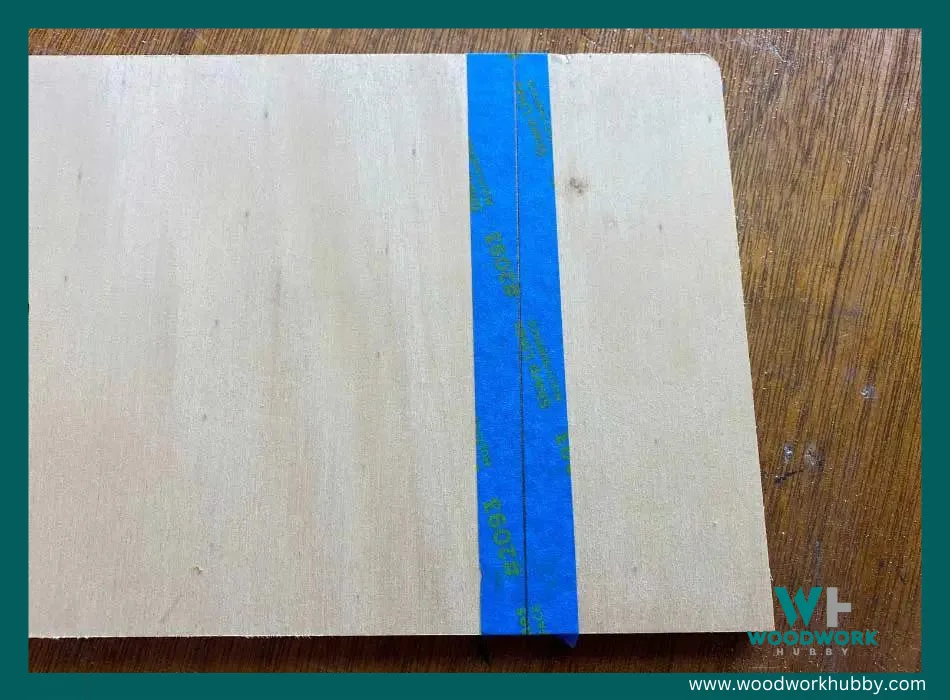
Place a strip of blue masking tape through the center of the plywood sheet where you intend to cut as shown in the above photo. Then, gradually cut over it. It will help you in preventing frayed edges. It operates by providing some resistance to tool vibrations. This minor step may provide you with the desired factory edge.
Only the paper masking tape should be used to avoid a grime layer on your edge.
6. Begin by cutting from the end
Rather than commencing at one end and ending at the other, you should start cutting at both extremes and converge in the center. Because of the nature of plywood and all other forms of wood, when you’re nearing the end of the cut, you’re more prone to get a nasty tear-out.
This method is better suited for CNC routers. It would be challenging to produce a straight cut with a free-hand saw like the circular one.
See my article on how accurate is a CNC router.
If you must make a long cut, ensure that the starting edge of the cut is well supported once it has been cut. If the offcut is left hovering, the uncut end might tear off before it gets accomplished.
Fix and Prevent Plywood Tear-Out with a CNC Router
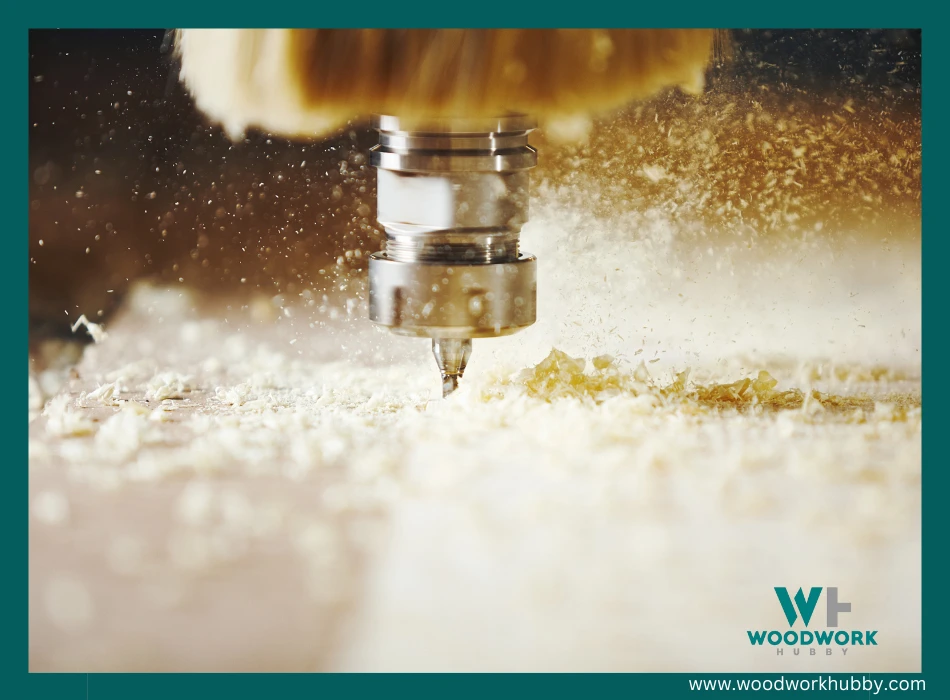
If you’ve ever cut with a CNC router, you know how important it is to avoid tear-out. This tool is best suited for precise, complicated geometries. That’s something you don’t want to screw up. Here are a few tips for keeping those passes clean.
1. Make use of a compression or down-cut bit
Consider utilizing a down cut or compression bit. These are wood-cutting bits designed specifically for CNC routers. They are intended to reduce splintering by reversing the direction in which the cutter tugs against the wood.
A down-cut presses the wood down, whereas a standard up-cut pulls the board up. Splintering is aided by pulling up. Compression bits attempt to draw towards the middle of the material such that neither the top nor bottom splinters.
2. Use sharp bits and stick to the carbide
You likely need a new bit if you’re getting a lot of splintering anywhere you cut. The reasons could vary from using a new CNC router bit to ensure that it is sharp to just trying out a different type of bits like a down-cut or compression.
Moreover, you should avoid HSS and commit to carbide. HSS dulls far too soon, whereas carbide can maintain its sharpness for much longer.
3. Make use of a backer board
A backer board supports the wood surface and can help to reduce tear-out. Certainly, the supporter cannot obstruct the cut. When clamped on the end grain, it allows you to cut parallel to the grain. However, you may alternatively employ your spoilboard as a backing board for the bottom of the cut, with another board stacked to safeguard the top.
Yet, the entire stack size would become unwieldy at some stage, so this may not be feasible.
4. Cutting through the risky spots
Climb cutting achieves several tasks that reduce tear-out and splintering. For one thing, it minimizes cutting forces, reducing the strain while tearing out the wood. Secondly, the chips get sliced into small C-shaped chunks. They have a thin end and a thick end.
Climb cutting thickens as the cut develops. The cutters are usually fat and get leaner with conventional cutting. They slam down with full force, which increases the likelihood of a tear-out.
Climb cutting occurs when the pinch roller pulls the workpiece into the cut. It’s conventional cutting if it’s pushing against the cut. If you use a handheld router, climb cutting can get excruciatingly inconvenient. The router tends to depart by itself. However, one of the benefits of CNC is that it regulates those forces, allowing you to do climb cuts wherever you choose.
See more on this at ProCarve – a wood routing & CNC cutting company based in Somerset.
5. Run distinct roughing and finishing passes
If the splintering is minor, a separate roughing and finishing pass can eliminate it entirely. The objective is to make the finishing pass considerably lighter than the roughing pass so that it clears the fragmented region but does not cause any new splinters.
This procedure may necessitate more than one finish pass. You might need to run several lighter passes (usually three to four passes). The lighter the pass (implying a smaller cut width or stepover), the lesser the chances of tear-out. That’s why using multiple lighter passes instead of one large, heavy pass could be the solution to these issues.
6. Execute an appropriate feed rate
Feeds and speeds are extremely significant in CNC. Run the feed rate that is appropriate for your cutter and material. You can refer to several feeds and speeds software that incorporate a slew of CNC router-specific capabilities. Explore the databases of several wood species, then progress to support for specialist router cutters such as compression, down-cut, and straight flute, and finally to other features.
7. Cut your entry by ramping in and slowing down
Plunge cuts are the riskiest approach to initiate the cut and are the most likely to produce tear-out. Ramping is a milder method and is thus favored. The caveat to this tip is that when employing compression and down-cut bits, you need to get them into the cut as quickly as possible so they can perform their job.
Pro tip- Cut the end grain cuts first, followed by the long grain cuts. This lowers tear-out and splintering significantly.
8. Prefer shallower cuts
Reduce the depth of the cut. The greater the depth of the cut, the more of the cutter’s helix is present in the cut. The helical shape is responsible for the upward pull that contributes to tear-out and splintering. As a result, decreasing the depth of the cut decreases the amount of helix that can transmit upward stresses.
Instead of a helix, a straight flute cutter is a better option. At the very least, it isn’t pulling up with any helix. It may still pull in a direction parallel to the cut, but there are other options in hand.
Are you looking for a CNC tool? Just a handful of machine tools can match a vertical mill for precision. Operators can benefit from a variety of benefits with a vertical mill, including a small machine footprint and high accuracy controls.
Conclusion – How To Fix And Prevent Plywood Tear-Out With CNC Router?
Plywood tear-out poses a prominent issue without any question. Based on the complexity of the materials you cut, you might not ever completely eradicate it, but now you are aware of ways to control or limit it. When you use the methods and tips outlined above, you will notice a significant reduction in tear-out. Always remember to take precautions and refrain from performing any inconvenient procedure.
About the Author:
Peter Jacobs
Peter Jacobs is the Senior Director of Marketing at CNC Masters. He is actively involved in manufacturing processes and regularly contributes his insights for various blogs in CNC machining, 3D printing, rapid tooling, injection molding, metal casting, and manufacturing in general.